Making of the GameChord
TL;DR: I made a USB keypad that's good for gaming and typing entirely with one hand.
So, remember back in February when I said that keyboard hacking seems like fun? Well, I finished this GameChord thing back in July after about 5 months of occasional work. But, I've been too busy drinking booze and playing video games to get my butt in a chair and write about it.
Let's see if I can fix that now...
The design
I started doodling with key layouts and came up with
this. Only 18 switches, but enough for gaming. At the
time, I was putting a lot of hours into Elite
Dangerous, so this felt promising as a spaceship control pad.
Over on builder.swillkb.com, I plonked in the JSON from Keyboard Layout Editor and came up with some SVG files that printed up nicely.
That gave me a paper mockup of a mounting plate for key switches. I had some clear keycaps, so I dropped them onto the paper to get a sense for how it would feel under my hand.
Of course, cats happen - so those keycaps didn't stay put for very long. But, that's okay. Nothing wandered off too far, and I got what I needed from the mess on my desk.
Making the case
Back when I first started thinking about building a keyboard, I assumed I'd send off whatever design files I came up with to a place like Ponoko and get the mounting plate made for me.
Prices at those places were just a bit higher than I liked, though. I also suspected things wouldn't work with my first attempt. I wanted to be able to iterate without it taking days or weeks to learn from my mistakes and refine.
That's when I remembered i3Detroit was just down the road. I'd been meaning to get over there for a couple of years: Among other things, the space has nice laser cutters that I really wish I'd used back when I butchered some plastic to make a terrible PC monitor case.
A month or so later, I'd gotten through the new member onboarding process and a few training sessions with the laser cutter. I had some acrylic sheets still on hand, so I gave my design a shot:
Pretty sure I had the power too high and the speed too low for the run in this video. But, the result was not too bad for a first attempt. I had a few dozen Cherry MX Clear switches to play with, so I snapped them into the plate and put on the keycaps I'd used in the paper mockup earlier:
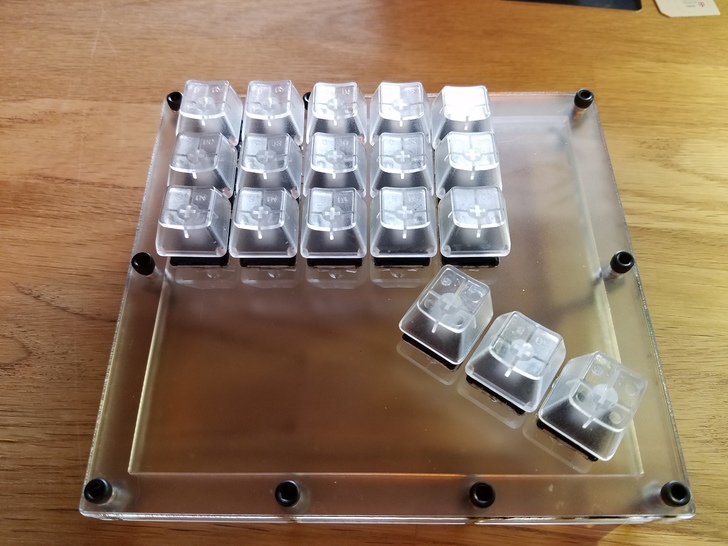
Still lots of work ahead, but I was feeling pretty accomplished after taking this little glamour shot. I even took it into an i3Detroit member meeting for show & tell.
Re-making the case
At this point, I'd already heard the term "kerf". Like a saw blade, the laser has a width that destroys material while cutting. You want that on the inside edge of something like a key switch mounting hole, in order to keep the dimensions correct. Unlike a blade, the laser is a cylindrical beam that passes through a lens to form something like an hourglass. So, the kerf's shape depends on the lens focal length and the conical section that intersects with the material.
Well, I didn't account for the kerf well enough in my first plate. All the key switches were wobbly. Some would just fall out if I flipped the thing over. Time for some of those iterations I figured I'd have to end up doing.
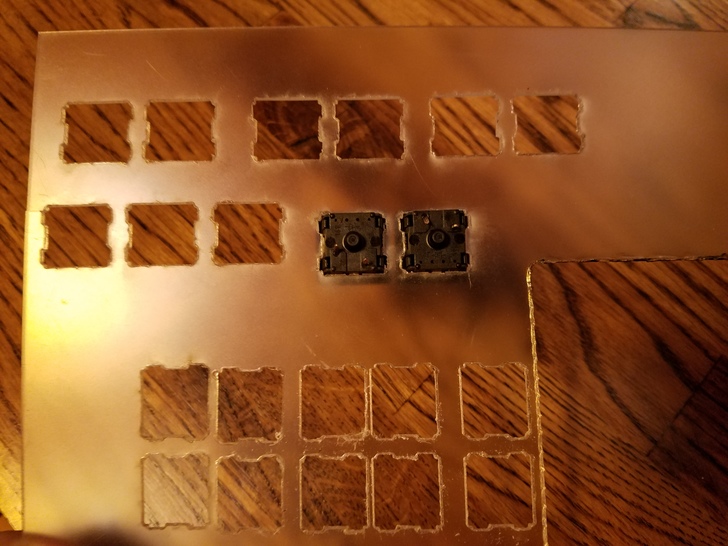
I know the saying is "measure twice, cut once" - but in this case it was easier to measure by cutting! I tried mounting holes with a sampling of kerf widths until I found one that matched the key switch tolerances. Not so snug that it cracked the plate, but not so loose that it wiggled or fell out.
Once I found a good laser focus and figured out the kerf, I attacked another sheet of acrylic with the laser to produce another iteration of the case.
Two changes you might notice: I added slots to glue in some socket headers, so I could unplug or replace the Teensy without soldering. I also found some relegendable keycaps on Massdrop - they have little removable covers that take 14mm paper squares. I figured that would come in handy for crazy key layouts I might come up with.
Wiring up the key matrix
I haven't learned how to design circuit boards yet, so I figured I'd just handwire this like I saw in the video. Only 18 switches, so how bad could it be? Turns out, it's rather annoying. Interesting exercise with my terrible old Radio Shack soldering iron.
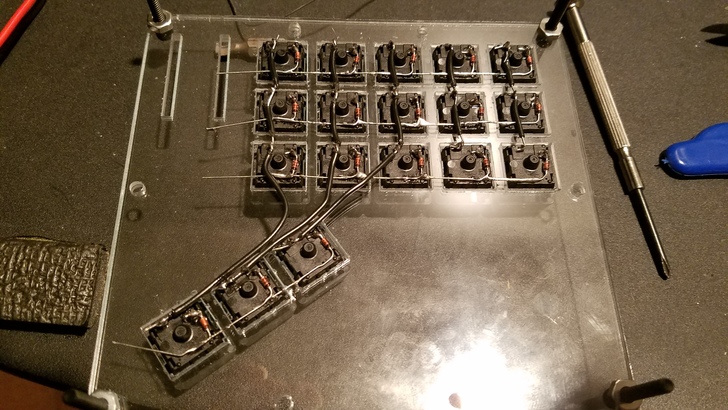
I think I'd much rather get over that PCB fabrication hurdle for when I try scaling this up to a 60% keyboard like my HHKB.
The technique here involves first building up rows of diodes across the right-hand pin of every key switch. The diodes serve to prevent ghosting when multiple keys are pressed.
Then, I stripped sections of wires to run as columns down the left-hand pin of the switches.
The remaining insulation ensures the column wires don't short against the row diodes.
Wiring up the Teensy
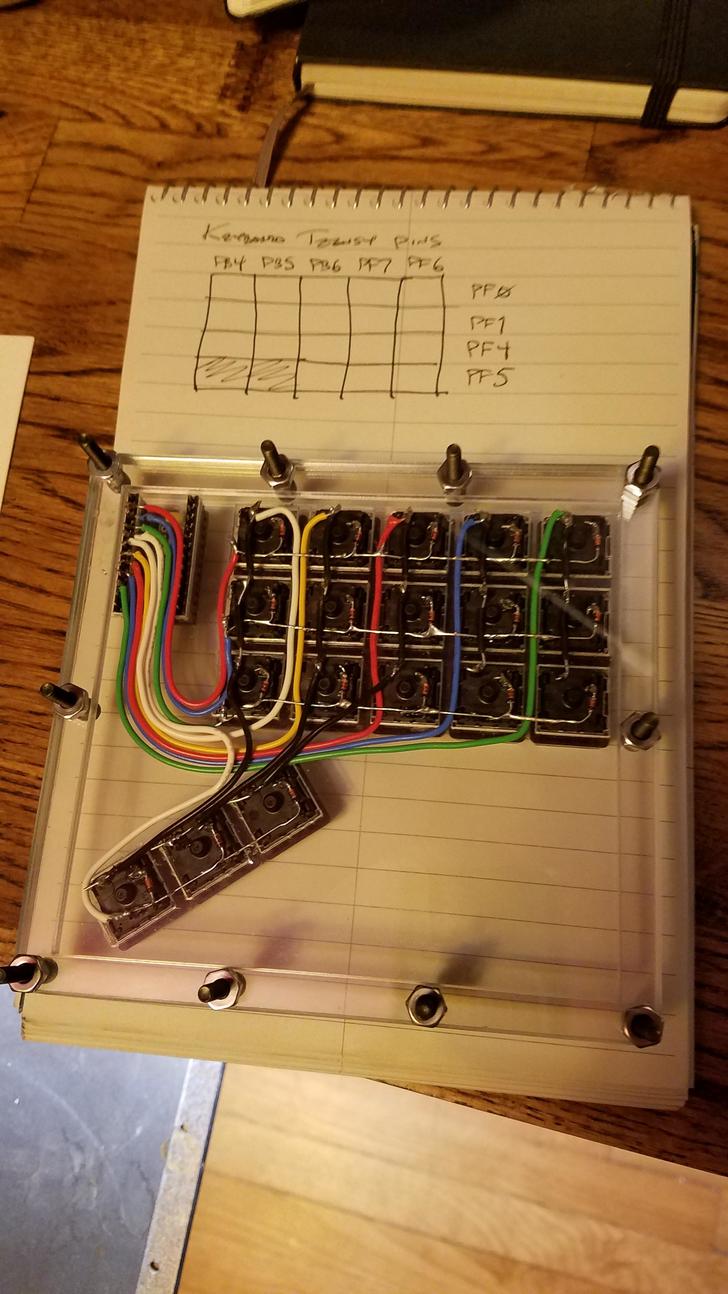
This matrix gives me 4 rows (counting the thumb switches) and 5 columns - or 9 I/O pins to scan 18 switches.
Except for magical PD6 - which is hardwired to an onboard LED - just about every pin is fair game on the Teensy for rows or columns.
So, I tried to pick a set that would be easiest to route wires. Since this case is transparent, I wanted to keep things visually interesting with different colored wires and a neat shape to the runs.
Of course, I botched things a bit and marred the acrylic by splashing solder and slipping with the iron a few times. But, maybe no one will really notice.
If I had to do this over again - and I still hadn't learned how to make a PCB - I'd probably try using something thinner like 30AWG repair wire. That seems like it would thread through the spaces much better, which would be even more important for a board with many more switches.
Programming the Teensy
I based the GameChord firmware on the great tmk firmware that seems popular on mech keyboard forums.
Building the matrix was easy: The firmware scans through rows (DF0, DF1, DF4, and DF5) by pulling each low in turn. The columns (DB4, DB5, DB6, DF7, and DF6) are set as "active low" pins - which means keys pressed in the current scan row get connected to ground and read as signals. So, I wrote the functions to manipulate & read the appropriate row & column pins, respectively.
It was almost too easy:
Holy crap. My attempt at setting up firmware for my newly wired DIY keypad worked first time. How does this happen. https://t.co/xWESzku4Lp
— Les Orchard (@lmorchard) June 25, 2016
From there, I built a dead simple key map with just enough keys to play Overwatch:
[#include](/tag/include) "keymap_common.h"
const uint8_t PROGMEM keymaps[][MATRIX_ROWS][MATRIX_COLS] = {
KEYMAP( ESC, 1, 2, 3, T, \
TAB, Q, W, E, R, \
LSFT, A, S, D, F, \
NO, NO, LCTL, SPC, C),
};
const uint16_t PROGMEM fn_actions[] = {};
I got it all working and had myself a nice evening of pushing carts and taking objectives.
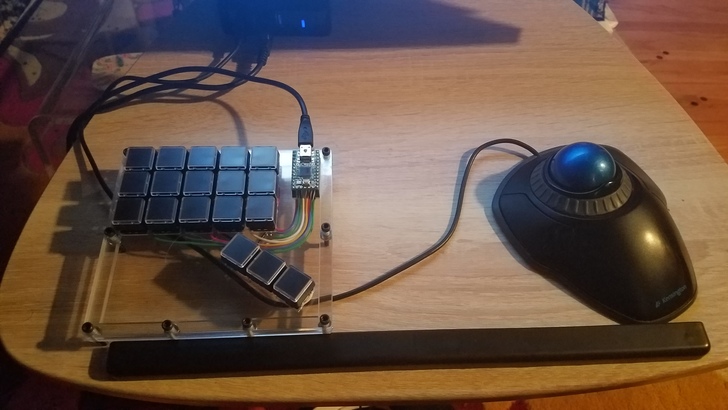
Going crazy with chording
I had all these relegendable keycaps and this crazy flexible tmk firmware - so I decided to try implementing a complex and fully impractical keymap based on chords with the thumb keys.
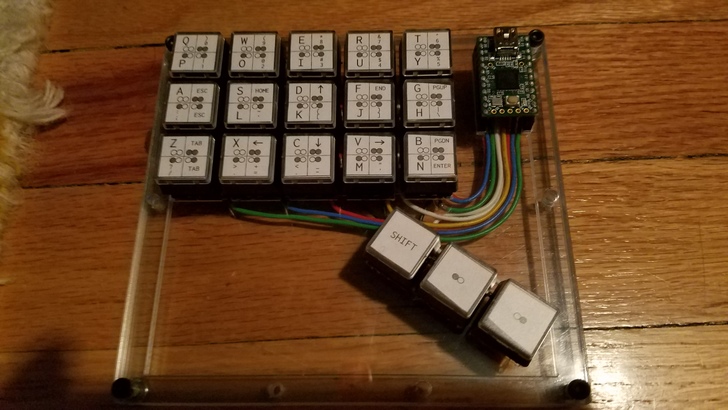
Given two thumb keys in combination, I can get 4 layers out of the other 15 keys - for a total of 60 keys. The firmware also lets me distinguish between keys held or just tapped, which gives me a few more layers or modifier keys.
Long story short, I can get most of the functionality of a regular keyboard out of just one hand. All I have to do is just get used to putting my left hand through some very awkward and uncomfortable contortions until I get up to full typing speed!
As I've written before, I do really like odd input devices. But, this got old fast. This isn't so much a practical peripheral as a thing I did because I could. It gave me an excuse to explore the firmware more and to use Inkscape to design some legends for my nifty keycaps.
Showing it off
And just to wrap things up, this happened:
I even have a project out in the @i3Detroit tent at #MakerFaireDetroit ! pic.twitter.com/v0goD3DCBk
— Les Orchard (@lmorchard) July 30, 2016
This was the first summer I went to Maker Faire Detroit as a Maker. I helped for a bit at the i3Detroit tent, mainly just standing and smiling at the front table as folks walked in. But, I had my little keyboard out there on a table, with a project card and everything.
It and I were only there for a handful of hours, but it's pretty satisfying to have actually gotten this thing done!